Customer: Waters Church, North Attborough MA
Customers Requirements:
The Church purchased a 75 year old manufacturing complex. The existing concrete had been shot-blasted and coated with epoxy. The customer wanted the existing floor coating to be removed. They wanted the concrete to be polished. The total area in our scope of work would be 40,000sf on 3 different levels.
Concrete Renovations Solution:
We specified an aggressive grind to remove the existing coatings and shot-blast lines. (16grit diamond on 3 54-inch diamond floor grinders. All left over epoxy would need to be removed from the low spots and joints to assure a uniform look. The floor would then need to be polishing up to an 800 grit, followed by a stain guard and burnish.
Our Process:
- Grind concrete floor with 16 grit diamond to remove coating and lines
- Jackhammer out all holes and voids to remove any coating left behind
- Grind concrete with 25,40,80 and 100 grit diamonds.
- Apply a concrete densifier to the entire slab
- Polish the concrete floor with 100,200,400 and 800 diamonds
- Apply a stain guard and burnish the floor
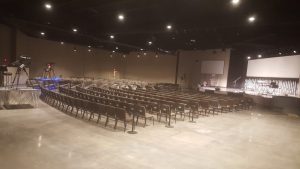
Customer: New Roc Speedway, NYC
Customers info and needs:
New Roc Speedway was started by Amusement Consultants. They operate four floors at this location. They have everything from bowling to ice skating. The owners have had great success with electric go karts at other locations. They decided to demo one of the ice rinks and use that area for the new go kart track. The removal of the ice rink left the concrete damaged. The rink walls had been sunk into the slab leaving a 6-inch deep trench, 900 feet long. There was also holes and exposed re bar everywhere. Another challenge to overcome was that the concrete was at two different levels. The two levels were off by 3-inches.
We knew what Amusement Consultants needed for a floor surface. We polished and coated over 35,000 sf at there location in Las Vegas, Nevada.
Our recommendation:
We specified patching the holes and trench with an epoxy repair mortar. The worn areas had to be saw cut , removed and troweled smooth. To lessen the elevation changes we would taper from high to low with a power troweled epoxy. The areas with exposed re bar needed to be cut back, the rebar removed and the area re-troweled with epoxy. The troweled areas would then be top coated with an orange peel epoxy.
Our scope of work:
- Square off areas to be repaired and saw cut.
- Jack hammer and scarify repair areas.
- Apply an epoxy primer to all areas to be troweled.
- Hand trowel all repairs.
- Diamond grind all areas to be tapered.
- Prime all areas to be tapered.
- Power trowel an epoxy mortar to provide a smooth taper.
- Diamond grind all troweled areas to reduce trowel marks.
- Apply a 100% solids epoxy grout coat.
The customer has very happy with the floor. The installation team that installed this project was from our Southwick, MA offices.
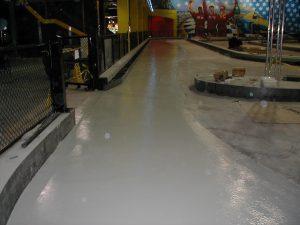
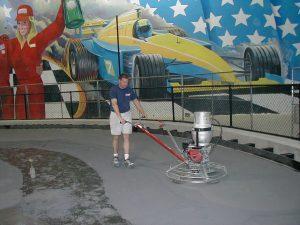
Customer: Hiromi Senju, Pleasantville NY
Customer info and needs:
Hiromi Senju is a Japanese, Nihonga Painter. He is known for his large-scale waterfall paintings. These paintings have been on display at the world’s top galleries and even the White House. We were contacted by Hiromi’s wife, Hiroshi. Hiroshi wanted us to come up with a floor system that would be a warm tone, resist all the solvents used in cleaning the studio floor and be seamless. The area to be coated was 3,500 sf.
Our recommendation:
We recommended a Tenant Company Epoxy/ Urethane flooring system. This system would be 47 mils thick. All the holes and voids would have to be filled with an epoxy repair matrix. To keep the tone of the studio calm, we choose a desert tan color.
Our scope of work:
- Grind floor to provide the proper surface profile.
- Patch all holes and voids with an epoxy repair matrix.
- Apply a high solids epoxy primer. At a thickness of 12 mils.
- Apply a 100% solids, self leveling epoxy at a thickness of 30 mils.
- Apply a chemical resistant urethane topcoat at a thickness of 4 mils.
We were very honored to be chosen to install the flooring for where Hiromi would be working.
Hiromi and Hiroshi were very kind to our installation crews. They were very happy with the result and had us install the flooring in the addition to the studio 5 years later. All floors at this location were installed by our Southwick, MA crews.

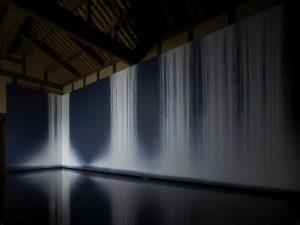
Customer: Affordable Housing, Kingston NY 40,000sf of concrete polishing.
Customers info and needs:
AH works with in cooperation with The State of New York to provide families with affordable housing. AH purchases old, abandoned factories and completely renovated them. They have been doing this for three generations. Most of the time the buildings have been vacant for many years. They work under the guidance of the local historical societies to preserve the history of these building. The historical society loves the look of the polished concrete floors. When dealing with frequent turnover in rental properties, polished concrete is the most cost effective floor surface. AH always specifies a polished floor when the substrate is concrete. In a rental environment, carpet wears, stains and needs replacing every time a new tenant moves in. A polished concrete floor is easier to clean, doesn’t have to be replaced and is stain resistant. It also meets ADA Accessibility Guidelines for Buildings and Facilities.
Our recommendation:
We recommended that all the concrete be polished to a level 4 finish. We also recommended that all the holes and voids be filled with a polishable concrete repair mortar. The joints would also have to be cut and caulked. The concrete around the isolation columns was over an inch higher than the floor. We would need to grind them level.
Our scope of work was:
- Grind the concrete around the isolation columns level.
- Saw cut, install backer rod and caulk all control joints.
- Grind the entire concrete floor surface with 16 grit diamonds to remove any existing glues.
- Fill all major holes, cracks and voids with a polishable repair mortar.
- Grind the entire concrete floor with 30/40, 60/80 and 120/140 grit metal bond diamonds.
- Apply a penetrating potassium silicate concrete densifier.
- Power scrub floor with a ride on floor scrubber.
- Polish the entire concrete floor with 100,200,400 and 800 grit, poly bond diamonds.
- Apply a polished concrete stain guard.
This job came out beautiful. Since this project we have completed another 50,000sf for AH and 4 jobs for this architect.
Customer: A 2. Z Storage, South Windsor CT
Customers info and needs: A 2 Z is a large and very modern self storage facility located in South Windsor Ct. They have hundreds of residential type units as well as large commercial spaces. In early 2017 a fire brook out in one of the units rented to an auto body shop. The fire destroyed the entire building. The building was later replaced but the concrete was badly damaged. The concrete was burned and had buckled and delaminated, leaving deep holes. The owner needed the floors fixed.
The total area to be repaired was 4,150 sf.
Our recommendation: We specified that the holes needed to be prepared using bush type jackhammers. The floor would be prepared using diamond concrete grinders. The holes would be filled with a urethane mortar and ground smooth after curing. The floor needed to have a 2-coat epoxy coating to seal the concrete.
Our scope of work:
- Remove all unsound, burned concrete using jackhammers.
- Fill all holes with a urethane repair mortar.
- Grind patches smooth using diamond grinders.
- Prepare concrete floor using Diamatic Grinders.
- Apply a 100% solids, epoxy floor primer.
- Apply a 100% solids, orange peel epoxy top coat.
This was a tough project to complete within the owners budget, but we did. The owner was very impressed and loves the new floor.
This floor was completed by a crew from our Southwick, MA location.
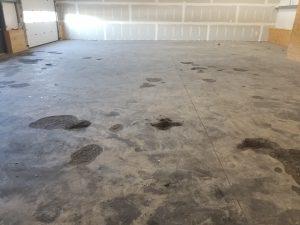
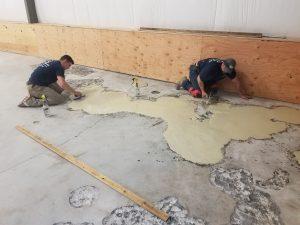